Introduction
In today’s fast-paced and technology-driven world, the importance of reliable cable assemblies cannot be overstated. These critical components serve as the lifelines of modern electronics, providing the necessary connections and power for a vast array of devices across multiple industries. From the intricate wiring in aerospace applications to the complex networks in telecommunications infrastructure, cable assemblies ensure that our digital and physical worlds remain interconnected and operational.
However, the significance of selecting the correct cable assembly for your specific project extends beyond mere connectivity. The right assembly can mean the difference between a highly efficient system and one prone to failures, a product with a long lifespan versus one that quickly becomes obsolete. The consequences of poor choices in cable assemblies can lead to system failures, safety hazards, and inflated costs due to maintenance and replacements.
Understanding the vital role of cable assemblies requires a look into their evolution. Historically, cable assemblies were simple and standardized, designed for generic applications with minimal variability. However, as technology advanced, so did the complexity and specificity of these components. Today, cable assemblies are highly specialized, and designed to meet precise electrical, mechanical, and environmental requirements.
The challenge, then, lies not in the scarcity of options but in the abundance. The market is flooded with a myriad of cable assemblies, each promising superior performance and reliability. This plethora of choices, while beneficial, can be overwhelming, underscoring the need for a thorough and informed selection process.
This guide aims to demystify the process of choosing the right cable assembly for your project. By understanding the components, defining your requirements, selecting appropriate materials, and ensuring compliance and quality, you can secure the reliability, efficiency, and safety of your systems. Let’s embark on this journey to make informed decisions that will enhance the performance and longevity of your projects.
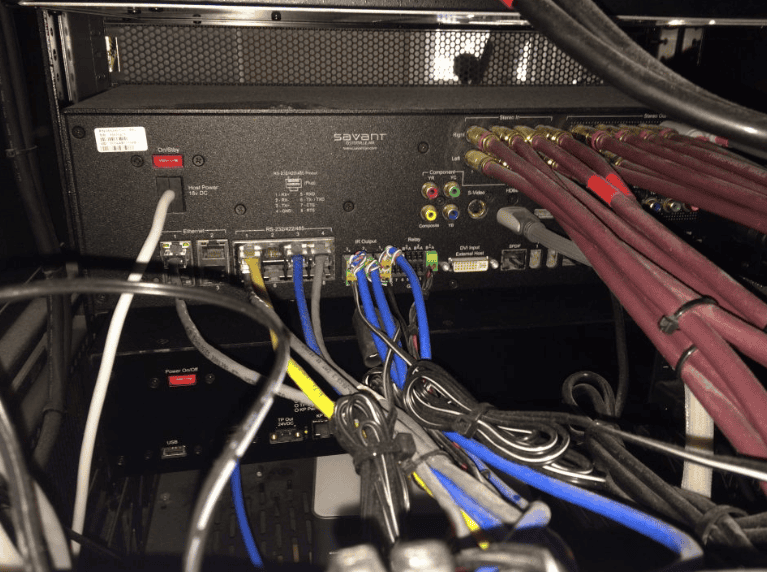
Understanding Cable Assembly Components
At the heart of every cable assembly lies its components. These are the building blocks that determine the performance, durability, and suitability of the assembly for specific applications. Let’s delve into the critical components of cable assemblies: conductors, insulation, shielding, and connectors.
Conductors
Conductors are the lifelines of cable assemblies, responsible for transmitting electrical signals or power from one point to another. The most common materials used for conductors are copper and aluminum, each with its own set of properties and applications. Copper, known for its excellent conductivity and flexibility, is the preferred choice for most applications, including high-speed data transmission and delicate electronic circuits. Aluminum, being lighter and less expensive, finds its use in power distribution applications, although its lower conductivity and durability compared to copper limit its use in more sensitive applications.
The configuration of the conductor, such as solid or stranded, also plays a critical role in its performance. Solid conductors, consisting of a single piece of metal, offer simplicity and lower costs but lack the flexibility and durability of stranded conductors. Stranded conductors, composed of multiple small strands twisted together, provide greater flexibility and resistance to breakage, making them ideal for applications involving movement or vibration.
Understanding the specific needs of your project is crucial when selecting the type of conductor. Factors such as the required current-carrying capacity, the electrical resistance, and the mechanical stresses the cable will face should guide your choice. It’s not just about choosing the highest quality or the most expensive option; it’s about finding the right fit for your specific requirements.
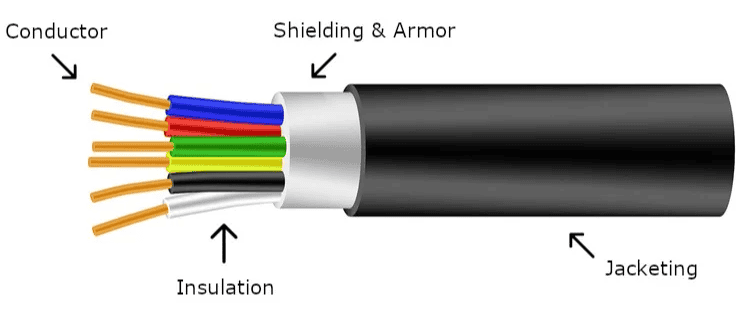
Insulation
Insulation in cable assemblies is critical for ensuring that conductors can effectively transmit power or signals without interference or loss. It serves the dual purpose of preventing electrical shocks and protecting the integrity of the cable from environmental factors. The choice of insulation material can significantly affect the assembly’s thermal resistance, electrical performance, and physical durability.
PVC (Polyvinyl Chloride) is a common insulation material known for its versatility, cost-effectiveness, and good insulation properties. It’s suitable for a wide range of applications but may not be the best choice for environments with high temperatures or where chemical resistance is necessary.
Teflon (PTFE), on the other hand, offers excellent thermal stability, chemical resistance, and minimal electrical loss, making it ideal for high-frequency applications or harsh chemical environments. However, Teflon’s superior properties come with a higher cost, making it crucial to assess whether its benefits are necessary for your application.
The selection of insulation material should be guided by the operational environment of the cable assembly, the electrical requirements, and the mechanical stresses it will endure. Factors such as exposure to high temperatures, chemicals, or the need for flexibility should dictate the choice of insulation to ensure longevity and reliability.
Shielding
Shielding is essential for protecting cable signals from electromagnetic interference (EMI) and radio-frequency interference (RFI), which can degrade performance. It’s especially important in environments with high levels of electrical noise or in applications requiring precise signal transmission.
Braid Shielding offers excellent EMI protection and is physically robust, making it suitable for environments where the cable may experience physical stress. However, its complexity can make it more expensive and less flexible.
Foil Shielding provides effective EMI and RFI protection and is lighter and more flexible than braid shielding, but it may not offer the same level of physical protection.
Choosing the right shielding involves balancing the need for signal integrity with the cable’s required flexibility and environmental exposure. It’s also crucial to consider the assembly’s overall size and weight, as these factors can be significantly impacted by the type of shielding used.
Connectors
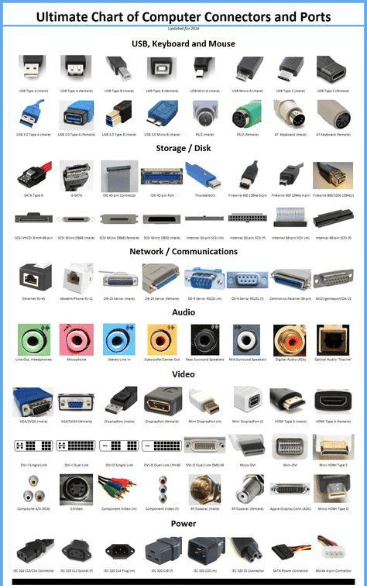
Connectors are the critical interface points of cable assemblies, enabling the connection to devices or other cables. The selection of connectors is paramount for ensuring compatibility, reliability, and performance.
USB, RJ45, and Circular Connectors are among the most common types, each serving different applications. USB connectors are ubiquitous in consumer electronics, offering a balance of data transfer speed and power delivery. RJ45 connectors are essential in telecommunications for wired networks, providing reliable high-speed connections. Circular connectors, used extensively in industrial and aerospace applications, offer robustness and can accommodate a wide range of signal types.
Choosing the right connector involves considering the application’s electrical and mechanical requirements, including pin count, current rating, and the need for environmental sealing. Compatibility with the devices or systems the assembly will connect to is also critical, requiring careful consideration of the connector type and specifications.
Selecting Materials
The selection of materials for both the cable and its connectors is fundamental to the assembly’s performance, durability, and applicability to specific environments. This decision impacts everything from electrical conductivity and signal integrity to resistance against environmental stresses like temperature, moisture, and chemical exposure.
Material Considerations: Evaluate conductivity needs, environmental exposure (chemicals, moisture, temperature extremes), and mechanical stresses (flexing, abrasion). For example, high-conductivity copper alloys might be ideal for signal transmission, while stainless steel or rugged plastics could be preferred for harsh environments.
Considering Customization
Customization allows for tailoring cable assemblies to the specific needs of a project, offering solutions that off-the-shelf products cannot. This includes custom lengths, connector configurations, and the incorporation of additional elements like strain relief or unique insulation materials.
Custom Solutions: Engage with manufacturers early in the design process to discuss custom requirements. Consider prototyping to test and refine the cable assembly design, ensuring it meets the project’s specific needs without compromising on performance or reliability.
Adhering to Compliance and Standards
Compliance with industry standards and regulations ensures that cable assemblies meet safety, quality, and performance benchmarks. This adherence can be critical for applications in regulated industries such as aerospace, healthcare, and telecommunications.
Standards and Certifications: Identify relevant standards (e.g., UL, CE, RoHS) early in the selection process. Work with manufacturers who can provide documentation and evidence of compliance, reducing risks and facilitating smoother project approvals.
Ensuring Quality Assurance
Quality assurance encompasses both the manufacturing process and the final product, ensuring that cable assemblies perform reliably over their intended lifespan. This involves rigorous testing for electrical performance, durability, and compatibility with other system components.
Testing and Validation: Look for manufacturers with established quality assurance processes, including in-house testing capabilities for electrical performance, flex life, and environmental resistance. Regular audits and certifications (e.g., ISO 9001) can also indicate a manufacturer’s commitment to quality.
Conclusion: A Strategic Approach to Cable Assembly Selection
Choosing the right cable assembly is a critical decision that requires a comprehensive and strategic approach. By understanding the components, defining requirements, selecting appropriate materials, considering customization, adhering to compliance, and ensuring quality assurance, projects can achieve not only technical success but also long-term reliability and efficiency.
Future-Proofing: The ideal cable assembly not only meets current needs but also anticipates future requirements and technological advancements, safeguarding against obsolescence and ensuring sustainability.
Contact us for a customized solution
For projects where the stakes are high, and the details matter, partnering with experienced manufacturers and suppliers who can offer guidance, customized solutions, and high-quality products is invaluable.
Contact our experts for personalized assistance in selecting the perfect cable assembly for your project. Let us help you navigate the complexities of cable assembly selection, ensuring that your project benefits from the reliability, efficiency, and innovation it deserves.