Introduction
Choosing the right electronic connectors is crucial for the reliability and performance of any electronic system. Connectors serve as the critical link between various components, enabling the transfer of power, signals, and data. This guide will help you understand the essential factors to consider when selecting electronic connectors for your applications, ensuring you make an informed decision that meets your specific needs. We’ll also highlight the importance of partnering with a reputable electronic connectors manufacturer.
1. Understanding Your Application Requirements
Identify the Specific Needs of Your Application
To begin, it’s essential to identify the specific requirements of your application. Electronic connectors come in various types, each designed for different purposes. The first step is to clearly define the type of application you need connectors for, whether it’s data transfer, power supply, or signal integrity.
Types of Applications
- Data Transfer: Used in computer systems, networking devices, and communication equipment.
- Power Supply: Essential for delivering power in industrial machinery, consumer electronics, and automotive systems.
- Signal Integrity: Crucial in high-frequency applications like RF and microwave systems.
Environmental Conditions
Understanding the environmental conditions is vital. Connectors must withstand the operating environment’s temperature, humidity, and vibration levels. For example, connectors used in automotive applications need to be robust against extreme temperatures and vibrations.
Industry-Specific Requirements
Different industries have unique requirements. Medical devices demand high precision and reliability, while industrial applications might prioritize durability and resistance to harsh conditions.
Table: Comparison of Electronic Connector Types and Their Specific Requirements
Connector Type | Application | Voltage and Current Ratings | Environmental Conditions | Signal Integrity | Durability and Reliability |
---|---|---|---|---|---|
Wire-to-Board Connectors | Household appliances, industrial machinery | Moderate to high voltage and current | Moderate temperature, low vibration | Moderate | High (suitable for frequent connections) |
Board-to-Board Connectors | Computer systems, communication devices | Low to moderate voltage and current | Controlled environment, low vibration | High (critical for high-speed data transfer) | Moderate to high (depends on application) |
Cable-to-Cable Connectors | Networking, telecommunications, portable devices | Variable voltage and current | Moderate temperature, moderate vibration | Moderate to high | High (suitable for flexible applications) |
RF and Coaxial Connectors | Antennas, broadcasting equipment, high-frequency systems | Low voltage, low current | Controlled environment, low to moderate vibration | Very high (essential for signal integrity) | Moderate to high (depends on usage frequency) |
Circular Connectors | Aerospace, military, heavy machinery | High voltage and current | Extreme temperature, high vibration, moisture | High | Very high (designed for rugged conditions) |
Rectangular Connectors | Industrial automation, medical devices | Moderate to high voltage and current | Moderate temperature, low to moderate vibration | Moderate to high | High (suitable for reliable, long-term use) |
Fiber Optic Connectors | Data centers, telecommunications | Very low voltage (optical signals) | Controlled environment, low vibration | Very high (critical for data transmission) | High (precise alignment required) |
USB Connectors | Consumer electronics, computers, peripherals | Low voltage and current | Controlled environment, low vibration | High (important for data transfer) | Moderate (depends on usage frequency) |
Power Connectors | Power supplies, industrial equipment | High voltage and current | Moderate to extreme temperature, vibration | Low to moderate | High (designed for reliable power delivery) |
IDC Connectors | Computer peripherals, networking | Low to moderate voltage and current | Controlled environment, low vibration | Moderate | Moderate (suitable for quick and secure connections) |
This table provides a detailed comparison of different types of electronic connectors, their typical applications, and specific requirements in terms of voltage and current ratings, environmental conditions, signal integrity, and durability. Use this table to identify the best connector type for your application based on these criteria.
2. Types of Electronic Connectors
Overview of Common Connector Types
Understanding the various types of connectors available can help narrow down your options. Here are some of the most common types:
- Wire-to-Board Connectors: These are used to connect a wire to a printed circuit board (PCB). They are common in household appliances and industrial machinery.
- Board-to-Board Connectors: These connectors join two PCBs, often found in computer systems and communication devices.
- Cable-to-Cable Connectors: Used to connect two cables, common in networking and telecommunications.
- RF and Coaxial Connectors: These are designed for high-frequency applications, such as antennas and broadcasting equipment.
Choosing the Right Type for Your Application
Each type of connector has its advantages and disadvantages. For example, wire-to-board connectors are typically more secure and durable, while cable-to-cable connectors offer flexibility and ease of installation. Consider your application’s specific needs to choose the right type.
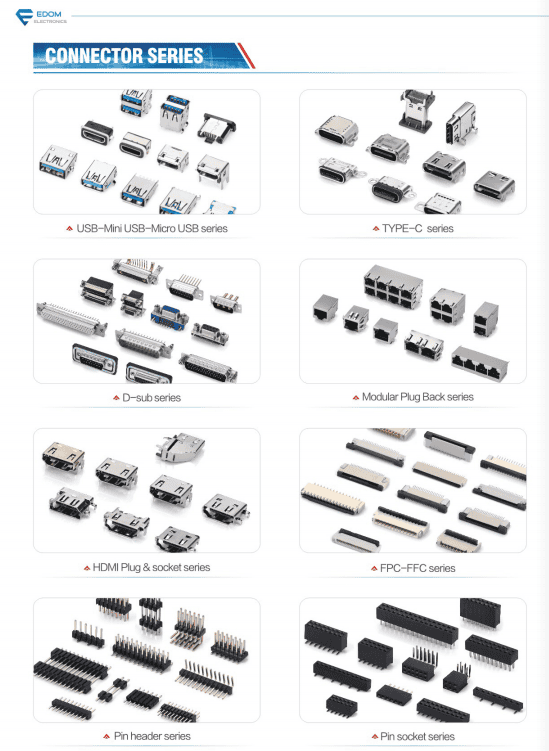
3. Key Factors to Consider
Electrical Specifications
One of the most critical aspects of choosing a connector is its electrical specifications.
Voltage and Current Ratings
Ensure the connectors can handle the required voltage and current for your application. Overloading connectors can lead to overheating and failure.
Signal Integrity Requirements
For applications requiring high-speed data transfer, maintaining signal integrity is crucial. Look for connectors designed to minimize signal loss and interference.
Shielding and Grounding
Proper shielding and grounding are essential to protect against electromagnetic interference (EMI) and ensure stable performance, especially in high-frequency applications.
Mechanical Specifications
Mechanical specifications determine the physical characteristics of the connector.
Connector Size and Shape
The size and shape of the connector must fit your design. Space constraints are common in compact electronic devices, making miniature connectors an ideal choice.
Durability and Reliability
Consider the durability of the connectors, especially in harsh environments. Look for connectors with robust housing and materials designed to withstand physical stress.
Mating Cycles and Ease of Connection
Mating cycles refer to the number of times a connector can be connected and disconnected before it fails. High mating cycles are essential for connectors that will be frequently used.
Insert a video demonstrating the importance of proper electrical and mechanical specifications.
Environmental Considerations
Connectors must be designed to operate under specific environmental conditions.
Temperature Range
Ensure the connectors can operate within the temperature range of your application. Some connectors are designed for extreme temperatures, suitable for automotive or aerospace applications.
Moisture and Humidity Resistance
For applications exposed to moisture or high humidity, connectors with water-resistant or waterproof features are necessary.
Resistance to Chemicals and Other Harsh Conditions
In industrial applications, connectors might be exposed to chemicals, oils, or other harsh conditions. Choose connectors made from materials resistant to these elements.
Table: Environmental Conditions and Corresponding Connector Features
Environmental Condition | Features | Example Connectors | Illustrative Description |
---|---|---|---|
High Temperature Environments | – Heat-resistant materials – High-temperature ratings – Thermal management solutions | – Circular Connectors (Aerospace) – Power Connectors (Industrial Equipment) | Connectors in a high-temperature industrial setting with temperature ratings |
Moisture and Humidity Resistance | – Waterproof or water-resistant seals – Corrosion-resistant materials – IP67 or higher ratings | – Circular Connectors (Outdoor Applications) – Industrial Connectors (Heavy Machinery) | Connectors in a humid or wet environment with IP ratings and waterproof seals |
Vibration and Shock Resistance | – Vibration-resistant design – Secure locking mechanisms – Ruggedized housing | – Circular Connectors (Military) – Rectangular Connectors (Automotive) | Connectors in a high-vibration scenario like automotive or military applications with vibration-resistant features |
Chemical Resistance | – Chemical-resistant materials (e.g., Teflon, silicone) – Sealed designs to prevent ingress – Enhanced durability against corrosive substances | – Industrial Connectors (Factories) – Custom Connectors (Specialized Equipment) | Connectors in a chemical plant or factory setting, highlighting chemical-resistant materials |
Controlled Indoor Environments | – Standard materials (plastic, metal) – Moderate environmental protection – Standard ratings (e.g., IP20) | – USB Connectors (Consumer Electronics) – Board-to-Board Connectors (Computers) | Connectors in a controlled environment like an office or data center, showing standard features |
This table provides a concise overview of different environmental conditions and the corresponding features required for connectors, along with examples and illustrative descriptions for better understanding.
4. Evaluating Quality and Compliance
Importance of Quality Standards
Quality standards ensure connectors meet specific performance and safety criteria.
Industry Standards and Certifications
Look for connectors that comply with industry standards and certifications, such as ISO, UL, or RoHS. These certifications ensure the connectors are safe, reliable, and environmentally friendly.
Ensuring Compliance with Regulations
Different industries have specific regulatory requirements. For instance, medical devices must adhere to strict standards for biocompatibility and sterilization.
Choosing a Reputable Electronic Connectors Manufacturer
Working with a reputable manufacturer is crucial for obtaining high-quality connectors.
Key Factors to Evaluate Manufacturers
- Experience and Reputation: Choose manufacturers with a proven track record in the industry.
- Product Range and Innovation: Look for manufacturers offering a wide range of products and continuous innovation.
- Customer Support: Reliable technical support and customer service are essential.
Importance of Manufacturer Support and Warranties
Reputable manufacturers provide warranties and post-sale support, ensuring any issues are promptly addressed.
Insert case studies or testimonials from trusted manufacturers.
5. Custom vs. Standard Connectors
When to Opt for Custom Connectors
Custom connectors are tailored to meet specific requirements, offering several benefits.
Benefits of Customization for Specific Applications
Custom connectors can be designed to fit unique specifications, ensuring optimal performance and reliability.
Cost Considerations
While custom connectors might have a higher initial cost, they can provide long-term savings by reducing failures and maintenance needs.
Advantages of Standard Connectors
Standard connectors are readily available and typically cost-effective.
Availability and Lead Times
Standard connectors usually have shorter lead times, making them ideal for projects with tight deadlines.
Cost-Effectiveness and Scalability
Standard connectors are often more economical, especially for large-scale production.
Insert a table comparing custom and standard connectors in terms of cost, availability, and suitability for different applications.
6. Future-Proofing Your Choice
Considering Future Needs and Upgrades
When choosing connectors, consider future expansions or upgrades.
Scalability and Adaptability
Choose connectors that can adapt to future technological advancements and increased performance requirements.
Technological Advancements and Trends
Stay updated with the latest trends and advancements in connector technology to ensure your choice remains relevant.
Planning for Long-Term Use
Long-term planning can save costs and reduce downtime.
Maintenance and Replacement Strategies
Establish a maintenance schedule and plan for eventual replacements to ensure continuous operation.
Working with Your Electronic Connectors Manufacturer for Ongoing Support
Maintain a good relationship with your manufacturer for continuous support and updates.
Conclusion
Choosing the right electronic connectors is a critical decision that impacts the performance and reliability of your electronic systems. By understanding your application requirements, evaluating key factors, and partnering with a reputable electronic connectors manufacturer, you can ensure you make the best choice for your needs. Remember to consider both current and future requirements to future-proof your selection.
Final Tips for Making the Right Choice
- Thoroughly evaluate all factors, including electrical and mechanical specifications, environmental considerations, and compliance with industry standards.
- Consider both custom and standard connectors based on your specific needs and budget.
- Partner with a trusted manufacturer to ensure high-quality products and ongoing support.
Call to Action: Contact a trusted electronic connectors manufacturer today to discuss your specific requirements and get expert advice on choosing the right connectors for your application.