Wire harnesses are an integral component of modern electronics, from our everyday appliances to the more complex medical devices we use. A wire harness is essentially a group of wires packaged together in a protective outer jacket that transfers power or data from one electronic component to the next. Wire harnesses can vary in their complexity, from simple point-to-point wiring solutions to more sophisticated, multi-branched cable assemblies.
In this article, we’ll take a closer look at wire harnesses, their various applications, and how they are manufactured. We’ll cover the different types of wire harnesses available, the materials used in their construction, and the various manufacturing processes involved.
Types of Wire Harnesses
Wire harnesses can be broadly categorized into four main types – point-to-point wiring, multi-branch wiring, cable assembly, and custom wire harnesses.
- Point-to-Point Wiring: This is the most straightforward type of wire harness and is most commonly used in smaller electronic devices. It consists of two or more wires that connect one electronic component to another.
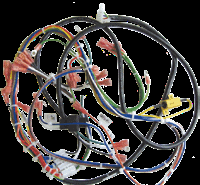
- Multi-Branch Wiring: This type of wiring is used for larger-scale, complex electronic systems where there are several electronic devices to connect. Multi-branch wiring is primarily utilized in aircraft and automobiles.
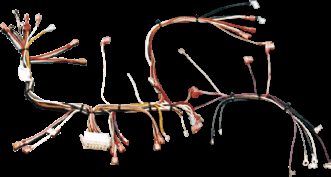
- Cable Assembly: Cable assemblies are made up of several individual wires that are bundled together with a jacket to form a single, larger cable.
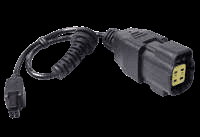
- Custom Wire Harnesses: As the name implies, custom wire harnesses are designed and manufactured to meet a specific application’s unique requirements.
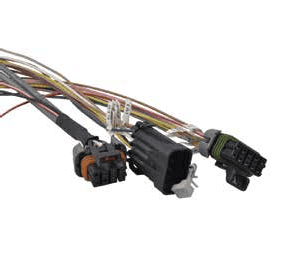
Components and Construction of Wire Harnesses
Wire harnesses are made up of several components, including wires, terminals, connectors, and outer jackets. The wiring components may be made from a variety of materials, including copper, aluminum, and silver. The outer jacket is typically made from thermoplastics like PVC or TPE.
The construction process itself involves several precision-based methods. Wires are first cut and stripped to the desired length, and the ends are fashioned with terminals. The wire strands are then bound together, often with an adhesive, before being tucked into the outer jacket.
Manufacturing Processes Involved in Producing Wire Harnesses
Manufacturing wire harnesses require several different processes, including cutting, stripping, crimping, soldering, splicing, and taping. Cutting and stripping involves trimming the wires to the correct length and removing the insulation at the wire’s end. Crimping is the process of affixing terminals to the stripped wire ends, while splicing involves joining multiple wires together.
Soldering is utilized when the wires don’t have terminals or need to be spliced together. The stripped wire ends are joined together with a heated soldering iron, which melts solder onto the wires, creating a permanent joint.
Splicing and soldering are often treated with insulating tape or sleeving and are then tucked into the outer jacket to form the finished wire harness.
Applications for Wire Harnesses
Wire harnesses are widely used in various electronic devices, primarily in the automotive, aerospace, and consumer equipment industries. In the automotive industry, wire harnesses are used for electrical applications such as engine management systems, entertainment, and lighting systems. In aerospace, wire harnesses are essential in powering all onboard systems, including communication, navigation, and entertainment systems.
In consumer equipment, wire harnesses are found in everything from household appliances like refrigerators and washing machines to medical devices such as MRI machines and X-ray equipment.
Benefits of Using Wire Harnesses in Electronic Devices
Wire harnesses offer several distinct advantages over other wiring methods. They improve safety by reducing the risk of electrical fires and other related hazards. They protect electrical circuits from extreme temperatures, moisture, and other environmental factors, extending the life of the electronic device.
Wire harnesses also allow for easy installation of an electrical system, reducing the required labor and time required. They require less maintenance and incur lower repair costs than wiring that’s installed individually without a harness.
Conclusion
Wire harnesses play a crucial role in powering the electronic devices we use every day, and their significance cannot be overstated. This article has provided an in-depth look at wire harnesses, including their various types, components, construction techniques, manufacturing processes, applications, and advantages.
When choosing a wire harness manufacturer, consider their experience, reputation, products, and services offered, manufacturing capabilities, and their commitment to quality and customer service. With the knowledge provided in this article, you’ll be better equipped to choose the right wire harness for your specific needs.
Wire harnesses are an essential component of electronic devices, and their importance cannot be understated. We hope this article has shed some light on the various types, construction methods, manufacturing processes, applications, and benefits of wire harnesses.
As a leading supplier of wire harnesses, EDOM Electronics has been providing customized wire harness solutions to our customers for many years. We are committed to delivering high-quality products that meet your exact specifications, with superior customer service and fast turnaround times.
If you’re in need of a custom wire harness solution, consider us as your preferred supplier. Our expert team of engineers and technicians will work closely with you to ensure we meet your unique needs and deliver a solution that exceeds your expectations. Contact us today to learn more about our wire harness solutions and how we can help you.