Every business that deals with cable assemblies have a nagging question: “How much should they cost?” The answer is not simple. Many factors determine the price of a cable assembly, and some can be completely out of your control. In this post, we will discuss the major factors that drive the cost of cable assemblies.
For starters, the main determinant of what a cable assembly will cost is whether they are custom-made or standard, off-the-shelf cables. If you are ordering custom cables then you should expect to pay more than if you were ordering standard cables. The reason for this is that making custom cables requires more effort in terms of design, labor, and production. However, there are other inherent factors that determine the cost of cable assemblies regardless of whether they are standard or custom cables.
Standard cable assemblies
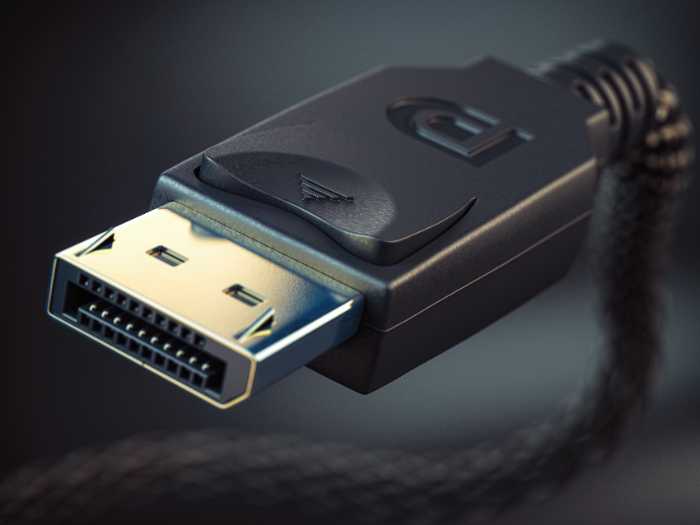
Standard cable assemblies are those that are provided by the manufacturer and typically follow the industry standard. The length, gauge, and connector type will all be predetermined by the manufacturer. Standard cable assemblies tend to be less expensive than custom assemblies.
Custom cable assemblies
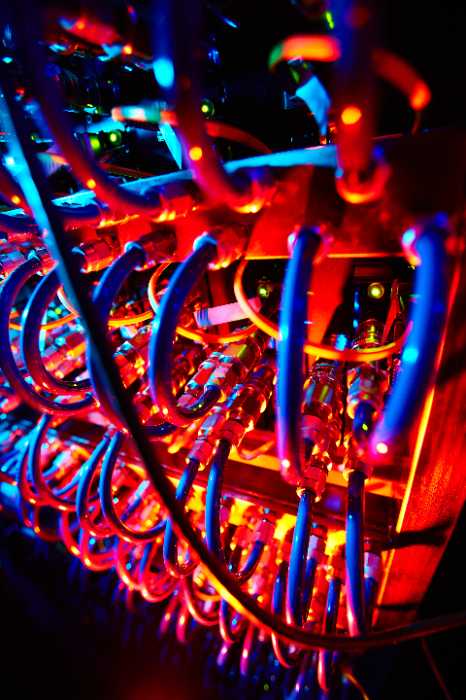
Custom cables are made according to order and can be designed to meet the specific needs of the customer. They can include a variety of connectors, lengths, and colors. The cost of custom assemblies will depend on how much customization is required. If you require a high level of customization then your cable assemblies will cost more. Generally, the pricing varies widely depending on project scope, complexity, and the type of materials used in making the cable assembly.
Factors that determine the cost of cable assemblies
There are many factors that go into the cost of cable assemblies, and it’s important to understand how each of them contributes to the final cost. By understanding these factors, you’ll be able to make more informed decisions when ordering your cables. Below are details about some of the most important factors that affect the cost of cable assemblies:
Length
The length of the cables is a major factor in determining price. The longer the cables, the more materials, and labor are required to produce them. This is one reason why custom assemblies tend to be more expensive than standard assemblies – they are typically longer than off-the-shelf cables. As a general rule, you can expect to pay an additional $0.50 – $0.75 per foot for each extra foot of cable ordered.
Gauge
The gauge of the cable is another important factor that affects the cost. Thicker cables are more difficult and expensive to produce than thin cables. This is because a thicker cable requires more materials, which means there is more metal to work with. Additionally, a thicker cable takes longer to manufacture, adding to the overall cost of the assembly. For this reason, there are more cost savings on thinner gauge cables than thicker gauge cables. Your selection should be based on how well they fit your intended use.
Raw materials used in cable assembly
Raw material makes up a significant portion of the cost of a cable assembly. The raw materials chosen for assembly will be based on the electrical performance expected by the assembly as well as the environment where the cable assembly will be used. The combination of the insulation, shielding and jacket materials of assemblies will determine the cost. A discussion with the supplier about the materials used in the cable assembly can result in useful cost-saving suggestions from their engineers.
Connector Type
The type of connector used on the cable assembly is yet another factor that affects the price. Different connectors will require different materials and manufacturing processes. Connector type typically does not affect cost unless it’s significantly different than what would normally be used in an off-the-shelf product like ethernet cables or USB cords. You should expect to pay more for assemblies with uncommon connector types.
Design
The design of the cable assembly also plays an important role in determining the price. Complex designs can increase costs dramatically depending on how many requirements must be met by your cabling solution provider (e.g., special colors, unique length measurements). Although some designs can offer a cost-effective solution, designs that require special materials or manufacturing processes will cost more.
Special Requirements
Extras/upgrades requested by businesses like cables with clasps that allow them to be hung on a wall can also significantly increase the cost of a cable assembly. This is because they require additional processes that are not typically used in standard assemblies. Often, these changes cannot be made without some kind of tooling investment by the supplier. Hence, customers have to pay more for assemblies with special requirements.
Manufacturing Process
The manufacturing process used to produce the cables is another important factor in determining price. There are a few different methods that can be used, and each has its own advantages and disadvantages. The most common methods are crimping, soldering, and molding:
Crimping
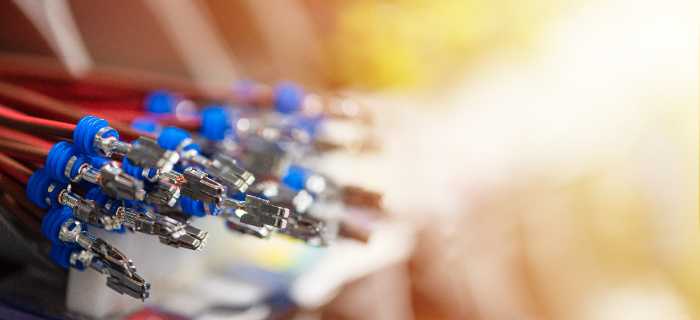
Crimping is the cheapest and quickest method, but it’s not as reliable as soldering or molding. This is because crimped connections are less sturdy and can become loose over time. This is why crimped assemblies are typically only used for temporary or disposable projects. You should expect to save costs with crimping cable assemblies.
Soldering

Soldering is a more reliable method than crimping because it uses heat instead of pressure to attach the wires and connectors. The downside to soldering is that it is not as quick as crimping since there needs to be enough heat available from the machine, which takes longer. Therefore, assembly times can range anywhere from 30 seconds – 20 minutes depending on how many connections need to be made at once (which varies widely). Solder-based cables are usually more expensive than crimped cables, but they are also more reliable.
Molding
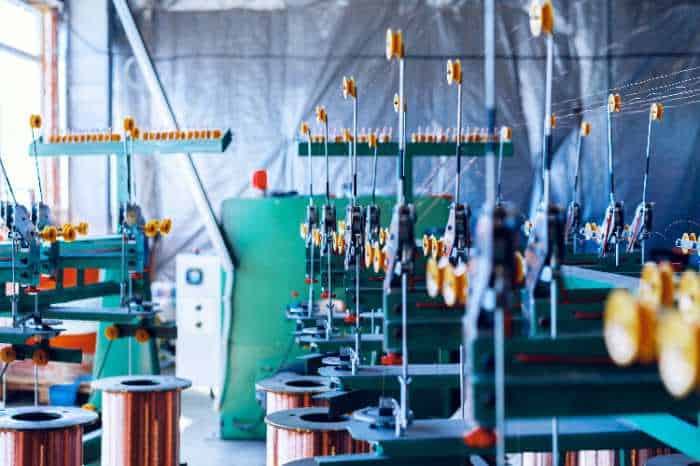
Molding is the most expensive and time-consuming method of manufacturing cable assembly. This is because the connector must be injected into a mold and allowed to cool before it can be used. The upside to molding is that it results in a very strong connection between the wires and connectors. Additionally, molded assemblies typically have a longer lifespan than crimped or soldered assemblies.
Why does custom cable assembly cost more?
As mentioned in our post, there are several reasons why custom cable assemblies cost more than off-the-shelf products. Most importantly, it takes longer to produce a custom assembly, which increases the supplier’s labor costs. Additionally, special materials or manufacturing processes may be required, which also raises the price. By understanding these factors, buyers can better anticipate how much they will need to pay for a custom cable assembly solution. Established cable assemblies suppliers like Edom Electronics will also offer quotes on your cable assembly request to help you estimate how much your cables will cost. You can contact them here to communicate your specifications and get a quick quote.