In the realm of electronics manufacturing, cable assemblies play a pivotal role in the functionality and reliability of a wide array of devices. Quality assurance (QA) in cable assembly manufacturing is critical to ensuring that products meet or exceed industry standards and customer expectations. This comprehensive article explores the essential checklist for QA in cable assemblies, detailing the methodologies and practices that manufacturers must adhere to for optimal product quality.
Comprehensive Design Review
Before moving into production, a thorough design review is paramount. This stage assesses the assembly design for manufacturability, functionality, and compliance with relevant standards and specifications. A detailed design review helps identify potential issues that could affect quality or performance, allowing for adjustments before production begins.
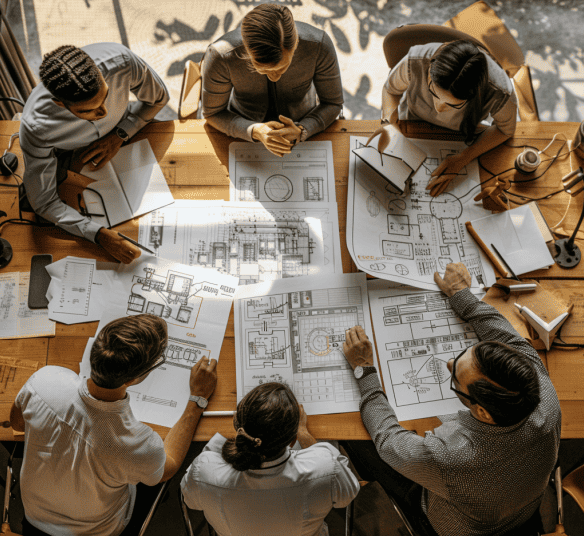
Material Quality and Compliance
The quality of the materials used in cable assemblies directly impacts the final product’s performance and reliability. It is crucial to verify that all materials, including wires, connectors, and insulating materials, meet the required standards and specifications. This includes checking for compliance with regulatory requirements, such as RoHS (Restriction of Hazardous Substances) and REACH (Registration, Evaluation, Authorisation, and Restriction of Chemicals).
Precision in Manufacturing Processes
The manufacturing process of cable assemblies requires meticulous attention to detail to ensure every component is produced and assembled accurately. This involves precise cutting, stripping, crimping, and soldering operations, followed by rigorous inspections to detect any defects or inconsistencies.
Electrical Testing and Validation
Electrical testing is a critical component of the QA checklist, ensuring that each cable assembly functions as intended. Tests include continuity checks, insulation resistance measurements, and hi-pot (high potential) testing to detect any electrical faults. This phase guarantees that the assemblies can safely and effectively conduct the required electrical currents and signals.
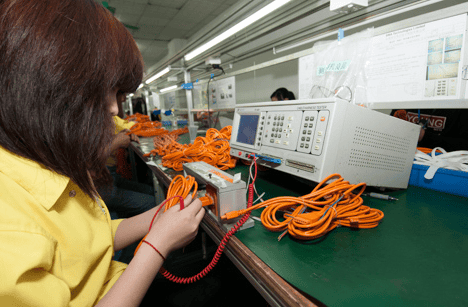
Mechanical and Environmental Testing
Beyond electrical performance, cable assemblies must withstand physical and environmental stresses. Mechanical testing assesses the assembly’s durability against flexing, twisting, and pulling, while environmental testing evaluates its performance under extreme temperatures, humidity, and exposure to chemicals. These tests ensure the assemblies are robust and reliable under various operating conditions.
Continuous Monitoring and Improvement
Quality assurance in cable assembly manufacturing is an ongoing process. Continuous monitoring of production data and feedback from quality checks allows for the identification of trends and potential areas for improvement. Implementing a continuous improvement strategy ensures that the manufacturing process remains efficient, and product quality consistently meets or exceeds expectations.
Conclusion
Ensuring quality in cable assemblies is a multi-faceted process that requires attention to detail at every stage, from design and material selection to manufacturing, testing, and continuous improvement. By adhering to this essential checklist, manufacturers can guarantee that their cable assemblies meet the highest standards of quality and reliability, satisfying industry requirements and customer expectations alike. Quality assurance is not just about meeting standards; it’s about setting a benchmark for excellence in manufacturing and fostering trust in the products and technologies that power our world.