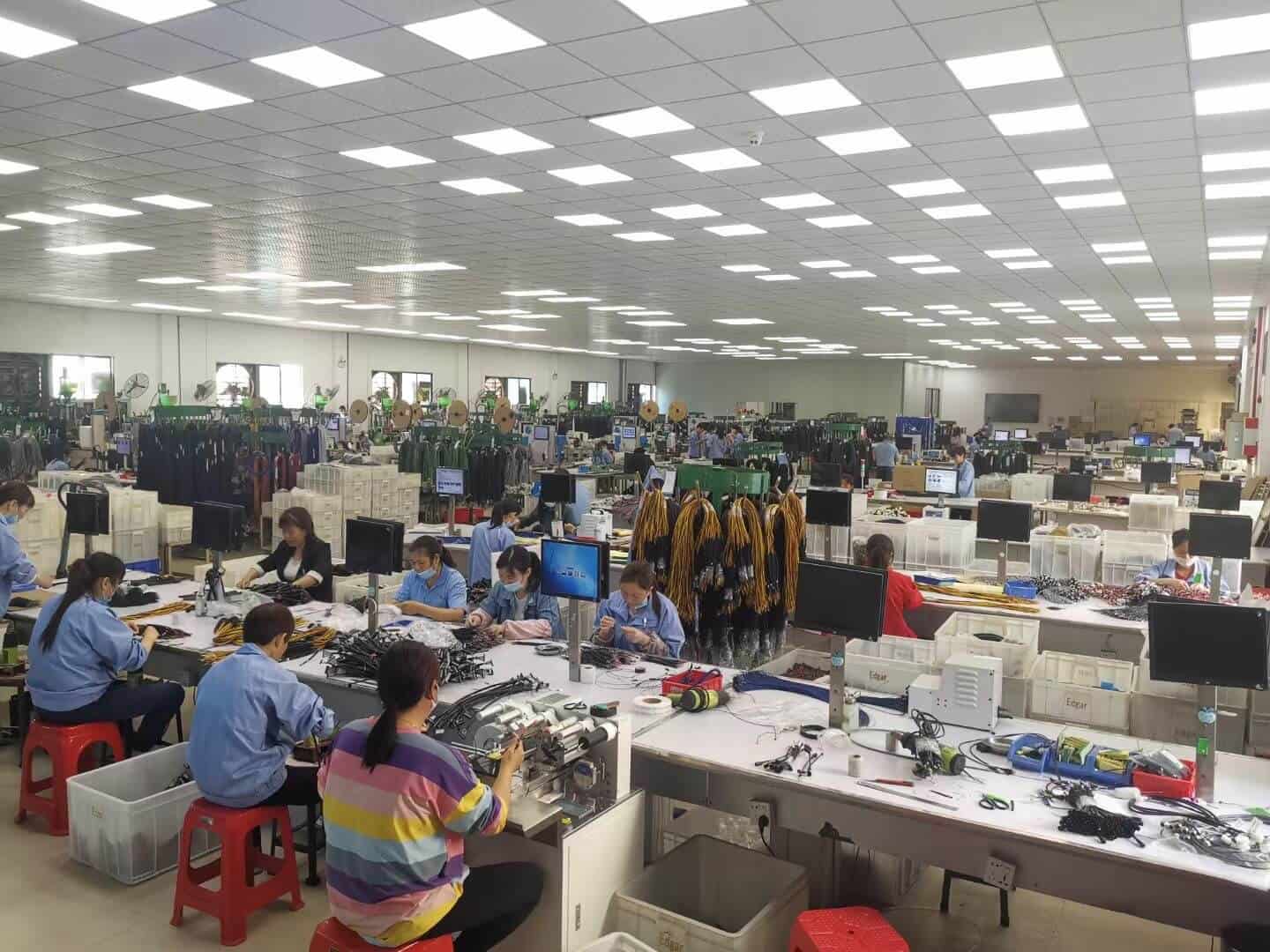
Custom Factory direct wire harness
EDOM Electronics is a professional wire harness manufacturer with over 20 years of experience in the industry. We produce various standard and custom wire harness, as well as other related products. With automatic machine production and full guarantee of quality and efficiency, we are confident that our customers will be satisfied with our work.
Table Of Contents For This Page
It is not easy to introduce all aspects of custom wire harness, so we have prepared a lot of information on this page for you to delve into. To make sure you can find the information you want quickly, we have prepared this content directory that will jump to the corresponding location when you click on it.
General Applications For Custom wire harness
A wire harness, also known as a cable harness or wiring loom, is an essential component in electronic and electrical systems, crucial for connecting various components. It consists of electrical cables or wires bound together, typically by straps or cable ties, enhancing manageability and reducing damage risk compared to loose wires. This assembly plays a vital role in transmitting signals or electrical power across different parts of a system.
General Hot Selling Products
In recent years, the rapid development of technology has made it possible to achieve 40Gbps transmission speed with 100W charging efficiency. The latest type C connectors can support both sides at once – that is to say, you can charge your phone wirelessly while uploading files from your computer!
Wanna dig deeper in custom wire harness?
Estimated Cost Analysis For wire harness
Please note that the final cost depends on the customized service you require. Creating an estimated cost analysis for a wire harness requires considering various factors that contribute to the overall cost. Below is a general outline of how you might structure an estimated cost analysis for a wire harness project。 Once all these costs are estimated, they can be summed to provide a total estimated cost for the wire harness project. It’s important to note that actual costs may vary, and the estimates should be reviewed and updated regularly to reflect changes in material costs, labor rates, and other variables.
General Applications For Custom wire harness

Wire and Cable:Calculate the cost of wire and cable based on length, gauge, type (e.g., copper, aluminum), and insulation material.Connectors and Terminals: Include the cost of all connectors, terminals, and any other hardware required. Protective Coverings:Account for the cost of any sleeving, conduit, or protective wrap. Labels and Markings: If the harness requires labeling, include the cost of labels or printing.
$0.01~10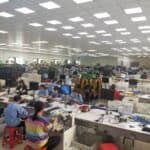
Assembly Time: Estimate the time it will take for workers to cut, strip, crimp, and assemble the wire harness and multiply by the labor rate. Quality Control: Factor in the time and labor associated with testing and inspecting the harnesses.
$1.5/H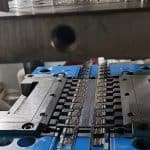
Equipment Usage: Allocate a portion of the cost of any specialized machinery used in the production process. Facility Costs: Include a percentage of the costs associated with the manufacturing space (rent, utilities, etc.). Tooling and Setup: If there are any special tooling or setup requirements, include these costs.
$500~$10000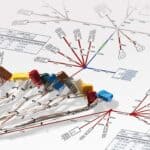
Design Time: Account for the time engineers spend designing the harness and creating specifications and schematics. Prototyping: If prototypes are made, include the costs associated with these.
$0~100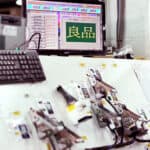
Compliance Testing: If the harness needs to meet certain standards or certifications, include the costs for testing. Failure Analysis: In case of testing failures, include potential costs for analysis and rework.
$0
Packaging Material: Include the cost of boxes, bags, labels, and protective padding. Shipping: Estimate the cost of shipping the harnesses to the client, considering weight, volume, and distance.
customer pay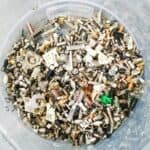
Waste and Scrap: Account for the material that is wasted or scrapped during the manufacturing process. Contingency: Add a contingency percentage to cover unexpected costs or overruns.
$0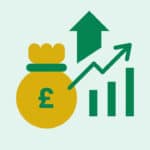
Markup: Include a markup percentage to ensure the company makes a profit on the wire harnesses.
5%~30%The Process Flow & Duration Estimation
The duration for each phase can vary based on the complexity of the wire harness, the volume of the order, and specific client requirements. The estimated times provided are based on a standard process flow and may be adjusted as per project needs.
Step 1: Design and Engineering (1-2 Weeks)
- Initial Consultation: Understanding client requirements and specifications.
- Design Phase: Creating detailed wire harness designs using CAD software.
- Engineering Review: Ensuring the design meets all technical and safety standards.
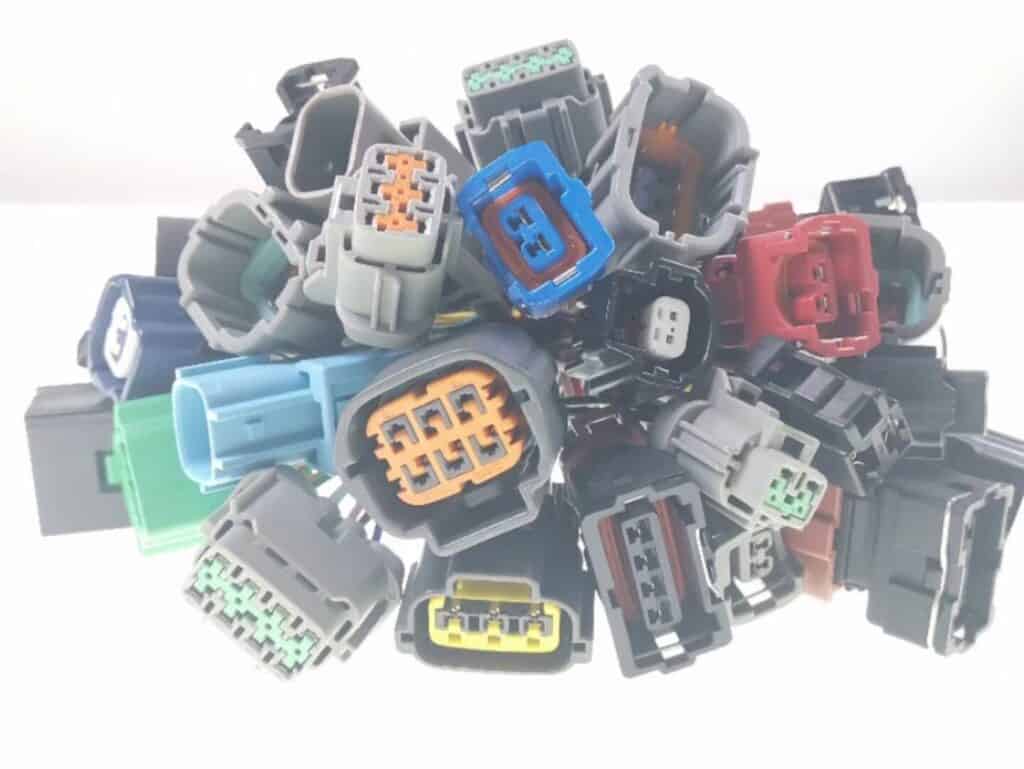
Step 2: Prototype Development (1-3 Weeks)
- Prototype Creation: Building a sample wire harness based on the finalized design.
- Testing: Conducting thorough tests to ensure functionality and safety.
- Client Approval: Presenting the prototype to the client for feedback and approval.
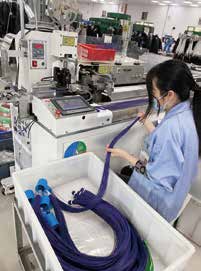
Step 3: Material Sourcing and Preparation (2-4 Weeks)
- Sourcing: Procuring high-quality materials like wires, connectors, and sheathing.
- Inspection: Quality check of materials to ensure they meet required standards.
- Preparation: Cutting wires to length and preparing other components.
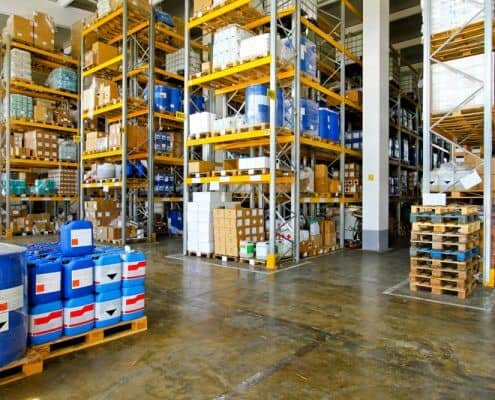
Step 4: Assembly (1-2 Weeks)
- Wiring: Assembling wires according to the design schematics.
- Connector and Terminal Fitting: Attaching connectors and terminals to wires.
- Bundling and Sheathing: Grouping wires together and adding protective sheathing.
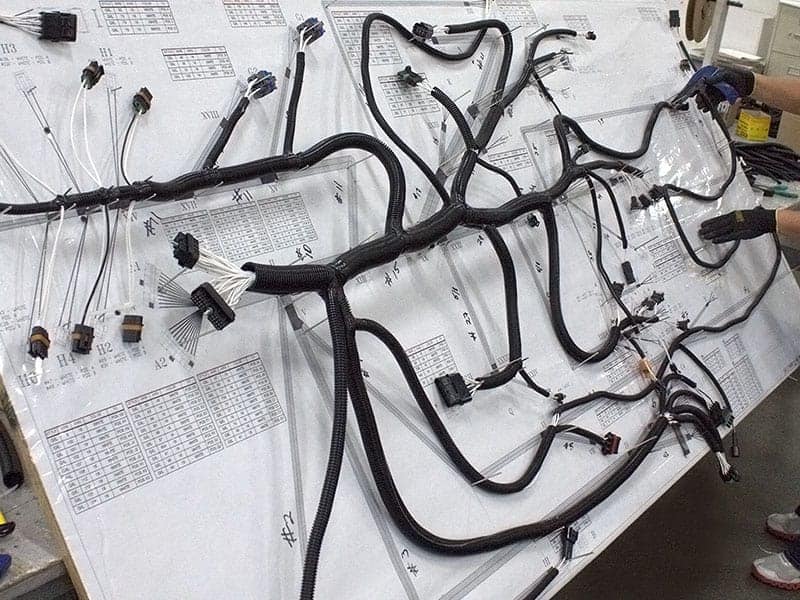
Step 5: Quality Control and Testing (1 Week)
- Inspection: Checking for any manufacturing defects.
- Electrical Testing: Ensuring all electrical connections are secure and functional.
- Safety Testing: Verifying the harness meets all safety standards.
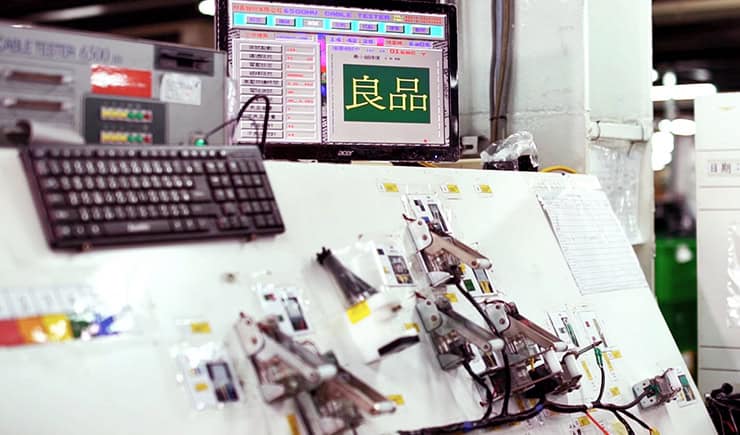
Step 6: Packaging and Shipping (1 Week)
- Packaging: Securely packaging the wire harnesses for shipment.
- Dispatch: Arranging for transportation and shipping to the client.
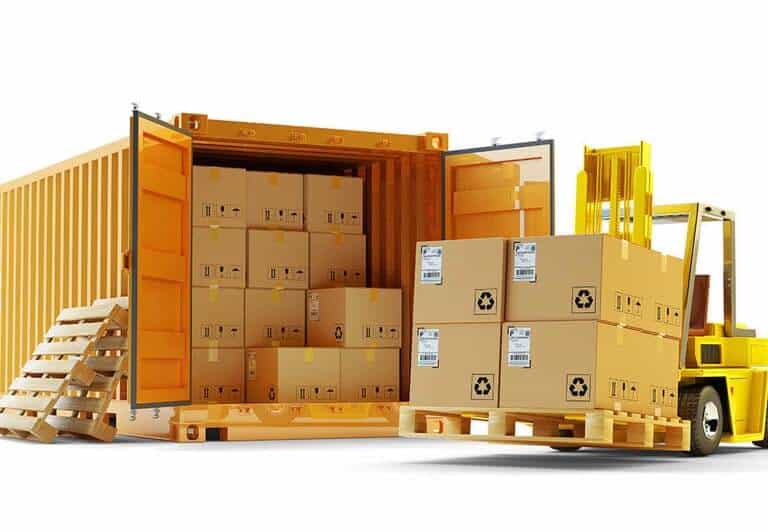
Step 7: Post-Delivery Support (Ongoing)
- Client Feedback: Gathering feedback from the client post-delivery.
- Support: Providing ongoing support and addressing any issues.

Want to know how to compress lead times?
We still have many ways to compress the delivery time. It’s just that the factories are still willing to do it on a standard delivery schedule. Do not like to rush the goods.
The Basic Knowledge About wire harness
There is a lot of industry knowledge here, and we have put it all in a blog post here.
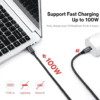
USB4 Cable Specifications: The Future of High-Speed Connectivity
Introduction As technology continues to evolve, the demand for faster, more efficient connectivity solutions has become critical for businesses and consumers alike. USB4, the latest iteration in the Universal Serial Bus (USB) family, addresses this
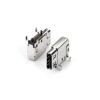
Introduction to USB Connector Versions
Understanding the Evolution of USB Connectors In today’s technology-driven world, USB (Universal Serial Bus) connectors are an integral part of our daily lives. From charging our devices to transferring data, USB connectors have evolved significantly
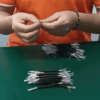
The Detailed Assembly Process of EDOM Electronics’ USB C to C Cables
At EDOM Electronics, we take pride in our meticulous approach to manufacturing high-quality USB C to C cables. Today, we’re giving you an exclusive look at the detailed steps involved in our cable assembly process,
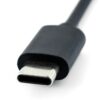
USB-C Connectors and USB-C Cables: The Future of Connectivity
The USB-C connector and USB-C cables are revolutionizing the way we connect and power our devices. As technology advances, these versatile connectors are becoming the standard for a wide range of electronics. In this comprehensive
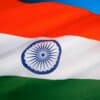
Top 10 Electronics Manufacturers in India
Introduction The electronics manufacturing industry in India has seen significant growth over the past decade, positioning the country as a crucial player in the global market. This growth is driven by increasing domestic demand, supportive
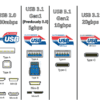
USB Connector and Cable Type Guide: The Ultimate Resource
In today’s digital age, USB connectors and cables are ubiquitous. They play a crucial role in connecting devices, transferring data, and powering our gadgets. Understanding the different types of USB connectors and cables is essential
The Common Pitfalls When Purchasing
What are the pitfalls of USB connectors when import from China, do you know? It is very complicated, but as long as you find a reliable supplier, follow the supplier step by step to confirm, this thing will also become very easy. The following are some common pitfalls.
- Choosing the wrong trade terms.
- Choosing unreliable suppliers.
- Not planning ahead.
- Not confirming samples.
- Not confirming delivery dates.
- No confirmation of pre-production samples.
Customers need to be clear about their needs and strict about what the factory must do. If it cannot be done, payment can be withheld. Factories need to always remind themselves whether the customer’s requirements have been met. Confirm various details and problems with customers in time.
Ensure that every step and process is completed according to the standards. No cutting corners. This is the way to build a long-lasting relationship with our customers. Let the customer be assured of our cooperation. Further expand the cooperation.
A Brief Self-Nomination, Why Choose EDOM Electronics?
Choosing EDOM Electronics means opting for a partner who excels in delivering high-quality electronic components and wire harnesses, tailored to meet your specific needs. Our commitment to innovation, robust supply chain management, and competitive pricing, coupled with over 15 years of industry experience, ensures not only product excellence but also exceptional customer service. With EDOM Electronics, you’re choosing a trusted partner dedicated to your project’s success, offering global reach with a personalized touch.
EDOM Electronics is a Chinese manufacturer specializing in the production of wire harness. With 15 years of experience in the connector industry, we have accumulated rich experience and resources in connectors. Our advantages are as follows.
- 2D & 3D drawings are available
- Free samples can be supported
- Fast delivery because of adequate material inventory
- One year warranty
The most important thing is that we insist on the customer first, and it is always our pursuit to make our customers happy and satisfied.
The FAQs About Wire harness
Please note that the final cost depends on the customized service you require, the specifications of the raw materials used, the relevant national laws, and the distance of transportation. Take the example of booking a tall container of products:
What is a wire harness?
A wire harness, also known as a cable harness or wiring assembly, is a systematic and organized arrangement of wires, cables, and connectors used to transmit signals or electrical power. They are designed to simplify the manufacture of a larger component and are used in various electronic and electrical applications.
What are the primary benefits of using a wire harness?
The main benefits include improved safety and reliability, simplified installation, reduced risk of electrical shorts, enhanced performance due to organized wiring, and easier troubleshooting and maintenance.
In what applications are wire harnesses commonly used?
Wire harnesses are widely used in automotive, aerospace, consumer electronics, home appliances, industrial machinery, and medical equipment, among others.
How are wire harnesses made?
The process typically involves cutting and stripping wires, crimping terminals onto one or both ends of the wires, inserting the wires into connectors, and bundling them together using various methods such as sleeving, taping, or tying.
Can wire harnesses be customized?
Yes, wire harnesses can be fully customized to meet specific requirements. This includes the length of wires, types of connectors, configuration of the assembly, and the inclusion of additional components like fuses or relays.
What materials are used in wire harnesses?
Common materials include copper or aluminum wires, PVC or rubber insulation, and plastic or metal connectors. The choice of materials depends on the application, including factors like temperature range, electrical requirements, and environmental conditions.
How do you ensure the quality of a wire harness?
Quality is ensured through rigorous testing, including electrical continuity tests, insulation resistance tests, and, in some cases, environmental tests like temperature or moisture resistance. Manufacturers also adhere to quality standards like ISO 9001.
What are the challenges in designing a wire harness?
Challenges include ensuring electrical safety, meeting specific size and weight constraints, selecting appropriate materials, and designing for ease of installation and maintenance.
How long does it take to produce a custom wire harness?
The production time can vary depending on the complexity of the design, the quantity needed, and the availability of materials. Generally, it can range from a few weeks to several months.